Vishnu Aishwaryan Subra Mani
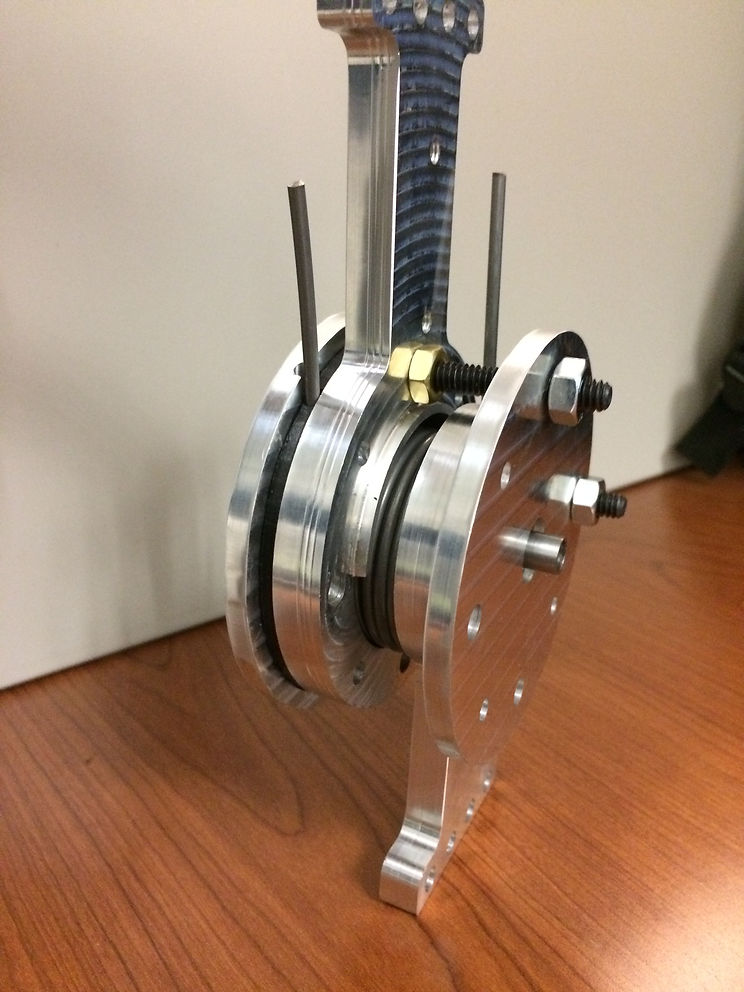
​
​​
​Current knee joints in the market were studied as a part of literature review using which a trade study was conducted to compare the mechanisms using weight, cost, power and holding torque as the critical parameters. An analytical approach was followed to choose a Wrap Spring Clutch/Brake mechanism for which I executed the mathematical design.
​
After evaluation a functional prototype was 3D printed to test the effectiveness of brake. The successful demonstration of its working helped me design a full system in SolidWorks whose results are shown in the background image. The crucial part of the mechanism was the arbor design over which the spring was wrapped.
Hence the components were manufacturing in-house to achieve these tolerance level to educate myself with the machines. The testing results showed that the knee joint was capable to withstand the designed torque limits. Several testings were conducted to characterize the behavior of the knee the results of the which can be seen in the following document.
The Objective of my Master's thesis was to design, manufacture and test a quasi-passive knee joint for an Assistive Exoskeleton
​CAD Software: Solidworks
​
CAM Software: Esprit
​
Control/Testing Software: MATLAB, Python
​​
Machines Used: 3D printers, CNC Machines, Laser Cutter
​
SKILLS LEARNED: 3D Printing, Clutch Brake Design, CAM, CNC Manufacturing, Biomechanics, Exoskeleton Controls and Architecture, Electrical Debugging, Human Subject Data, Kinematics, Dynamics
​
​​
Publications:
-
Vishnu Aishwaryan Subra Mani, Nathaniel Goldfarb, Gregory S. Fischer, "Design, Development and Characterization of a Wrap Spring Clutch/Brake mechanism as a knee joint for an Assistive Exoskeleton", ASME- IDETC-CIE 2020 - CAPPD TECHNICAL COMMITTEE BEST PAPER AWARD .
-
Vishnu Aishwaryan Subra Mani "Design, Development and Characterization of a Wrap Spring Clutch/Brake mechanism as a knee joint for a Hybrid Exoskeleton", M.S. Thesis, Worcester Polytechnic Institute.
​
​
ASME CIE 2020 Technical Talk
​
​
​
​